The Inrotech-Classic is a mobile welding robot primarily designed for the shipbuilding industry, specializing in welding webs, girders, and bulkheads on flat panels within open block assemblies. Utilizing Inrotech’s advanced SensLogic technology, the robot autonomously identifies structures and performs welds without the need for manual programming or CAD drawing transfers.
Operating the rail-guided Inrotech-Classic is exceptionally straightforward. The operator places the welding robot on its rails near the welding task. To initiate welding, only two simple inputs are needed: selecting the welding direction (right or left) and specifying the number of jobs. The system then performs a brief sensing sequence using a laser sensor to accurately identify the object’s geometry.
In open block assembly welding for shipbuilding, the Classic Rail is conveniently placed on the panel plate, allowing the robot to weld all joints up to a height of 1.5 metersโcovering more than 90% of the weld meters in an open shipbuilding block.
Reversing the Approach for Offshore Applications
The robot’s versatility and ease of use make it applicable to a range of industries beyond shipbuilding. In offshore contexts, welding beams and pancake structures require high precision and efficiency due to complex geometries and challenging installation environments. A key feature enhancing its performance is its modular, lightweight rail system.
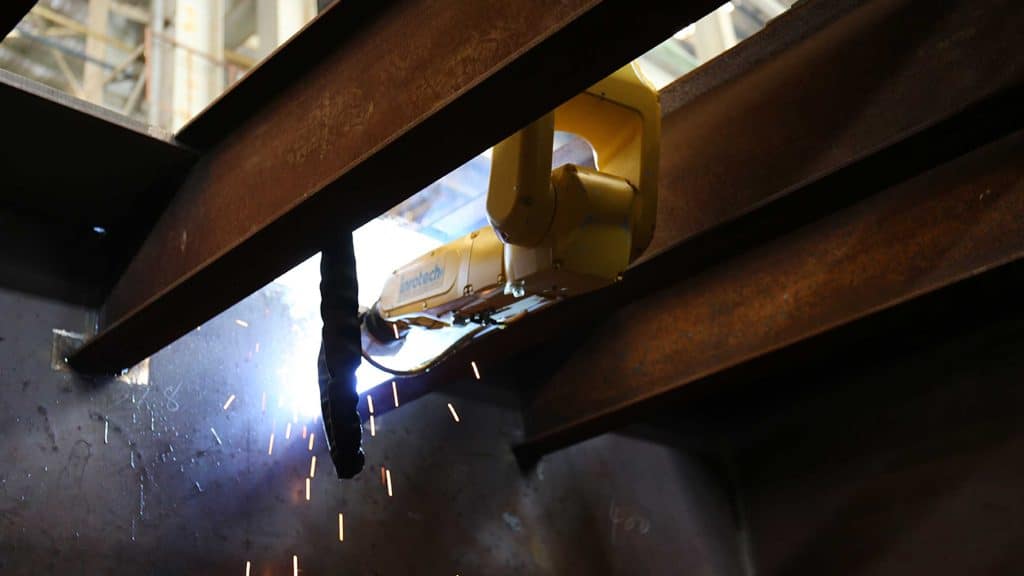
Unlike watertight ship structures that prioritize longitudinal strength, offshore and certain bridge structures often require cubic strength. Here, the Inrotech-Classicโs application approach is reversed compared to shipbuilding. The rail is positioned on the top of the cubic structure, allowing the robot to reach beneath the rail to perform vertical (PF/2F) and overhead (PD/4F) welds, efficiently joining crossing stiffeners and beam flanges.
Modular Lightweight Rail System
The Inrotech-Classic rail system offers exceptional flexibility, with modular extensions to accommodate varying workpiece sizes and configurations. This adaptability is particularly advantageous for welding pancake structures with complex geometries and spatial constraints. By positioning the rails above the beams (as illustrated in the image), the robot can execute continuous welds along extensive sections, minimizing stops and manual adjustments.
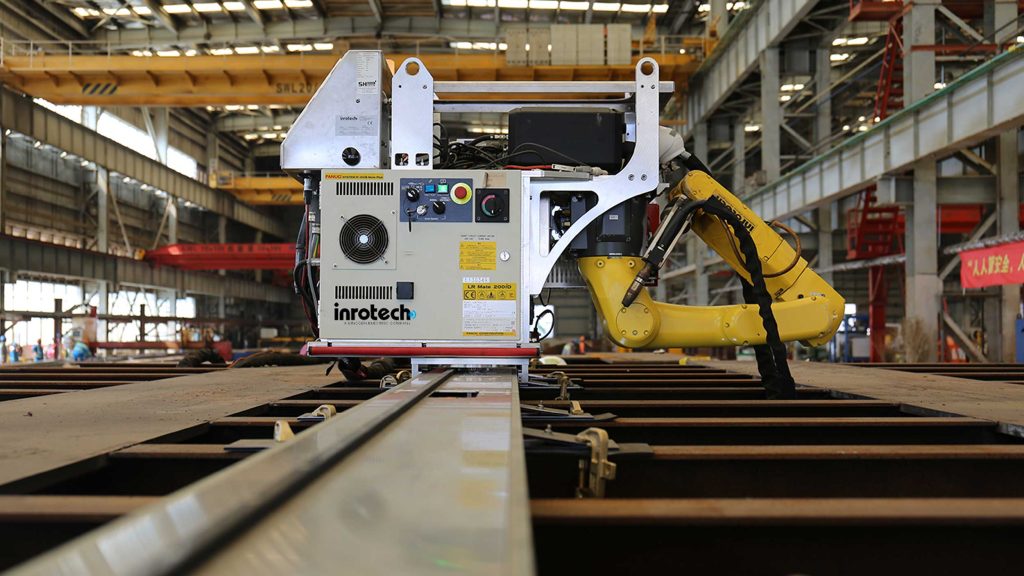
The console is propelled along the rails via a Fanuc servo motor and a gear-tooth rack system. You simply swivel it 180 degrees, enabling welding on both sides of the rail.Unlike its standard operations, the Inrotech-Classic can perform essential overhead welds crucial for constructing large pancake structures. This continuous workflow not only accelerates welding but also ensures consistent weld quality across the entire structure.
Advancing Double Hull Shipbuilding
For shipyards constructing double hull vessels, the Compact-Classic facilitates an optimized building method: assembling all parts of a double hull structure in one phase and welding in the next. This approach significantly reduces heat distortion and eliminates concerns about welding gaps.
If you are interested in closed double hull robot welding, thenย please contact Inrotech for more details.
Key Benefits of the Inrotech-Classic
โข High Arc Ratio and Density: Operators can manage up to six Inrotech-Classic units simultaneously, significantly boosting arc time and welding arcs per section with minimal investment.
โข Seamless Integration: The robot’s design ensures easy implementation into existing facilities without requiring layout changes, enabling swift deployment without operational disruptions.
โข Adaptability to Production Fluctuations: Without reliance on pre-made programs, the robot adapts to varying workloads. Shop foremen can flexibly allocate robots across different sections as needed.
โข User-Friendly Operation: An intuitive, icon-based touch panel interface requires no specialized training or prior programming experience, allowing efficient management of multiple units.
โข Independence from Engineering Support: The SensLogic technology enables autonomous structure recognition and welding execution, reducing the need for engineering input and CAD data.
โข Proven Performance: With a track record of reliability in global shipbuilding applications, the Inrotech-Classic demonstrates versatility and resilience in demanding industrial environments.
These features collectively establish the Inrotech-Classic as a cost-effective, flexible, and highly efficient solution for enhancing welding operations across diverse industries.